Case Study – University of Delaware
The University of Delaware’s Center for Composite Materials (UD-CCM), founded in 1974, has been internationally recognized as a center of excellence for interdisciplinary research, education and technology transfer in the science and engineering of composites. Utilizing over $25M in state-of-the-art equipment housed in 52,000 sq. ft. of laboratories, UD-CCM is a leader in university, industry and government partnerships that innovates new materials, synthesis, and characterization methods, processes, and automated manufacturing methods, including design and prototype development using modelling and simulation software tools.
Over the course of its nearly 50-year history, UD-CCM has been at the forefront of cutting-edge composite materials research and the development and optimization of composite manufacturing processes. The Dia-Stron automated LEX-LDS system was acquired in support of the Materials in Extreme Dynamic Environments (MEDE) program sponsored by the Army Research Laboratory. The focus of the MEDE program was the development of multi-scale modelling tools that spanned length scales from the atomic to continuum level. Critical to this program was the development of novel characterization tools for the measurement of fiber tensile properties and fiber/resin adhesion to generate experimental inputs for and validation of the computational tools under development.
The Dia-Stron system was used extensively to quantify the scaling of fiber strength distributions from 20-30mm down to 500µm gauge lengths and to assess the effects of weaving and sizings on strength retention. The automated testing features were essential to generate fiber statistical strength distributions for predicting composite strength. These unique testing capabilities continue to be used in our MEDE programs that focused on materials design of interphases using a physics informed machine learning approach driven by molecular dynamics models and experimental methods to synthesize and scale-up the application of fiber sizings.
In addition, these unique capabilities are now being used to support many other programs, including:
1. The development of the novel Tailorable universal Feedstock for Forming (TuFF) process. The TuFF technology enables fabrication of composite blanks composed of highly aligned short fibers that provide full translation of strength comparable to continuous fiber prepreg but can be formed easily into complex shapes using processing techniques (stamping) usually associated with metals. The Dia-Stron system is utilized to evaluate the tensile properties of the incoming fiber materials. The original development of TuFF process was funded through a multi-year DARPA program and continued optimization is funded through various agencies, including AFRL, ONR and ARL.
2. A DOE funded initiative to demonstrate closed loop recycling of TuFF-based composites, where the Dia-Stron system is used to evaluate the tensile properties of recycled carbon fiber materials over the course of multiple recycling iterations.
3. A NASA funded University Leadership Initiative program looking at the development of autonomous flying vehicles for commercial applications. In this program, one of the research tasks was to develop a new experimental method to map the distribution of defects along the fiber length to predict flexural and tensile strength which was validated using the Dia-Stron system. These defect maps are used to determine the maximum rate of material throughput while mitigating the risk of fiber breakage.
Critical to the success of these various research initiatives is the ability to rapidly and accurately assess the tensile properties of the incoming fiber feedstock. Equally important is the ability to quantify potential changes in fiber properties that occur at different stages in the manufacture of composite materials or recycling process. The Dia-Stron automated LEX-LDS system has greatly improved testing through-put, enabling relatively rapid assessment of statistically relevant sample sizes (60-100 specimens), compared to traditional single filament testing techniques. To date, the system has been used to evaluate a wide variety of carbon, glass, and polymer textiles, in service of the UD-CCM’s research initiatives.
UD-CCM has historically had an excellent relationship with Dia-Stron area representatives, and we feel confident that we receive training, consultation or advice on these systems whenever needed. We also have a valued partnership with the Dia-Stron team worldwide and can discuss any issues, considering they are based in the UK. We have a variety of instruments in the lab and the LEX-LDS is one of the most frequently used. We anticipate the Diastron LEX-LDS system will continue to play a critical role at UD-CCM for ongoing research and process development purposes.
Tekin Ozdemir, Postdoctoral Researcher
University of Delaware, Center for Composite Materials
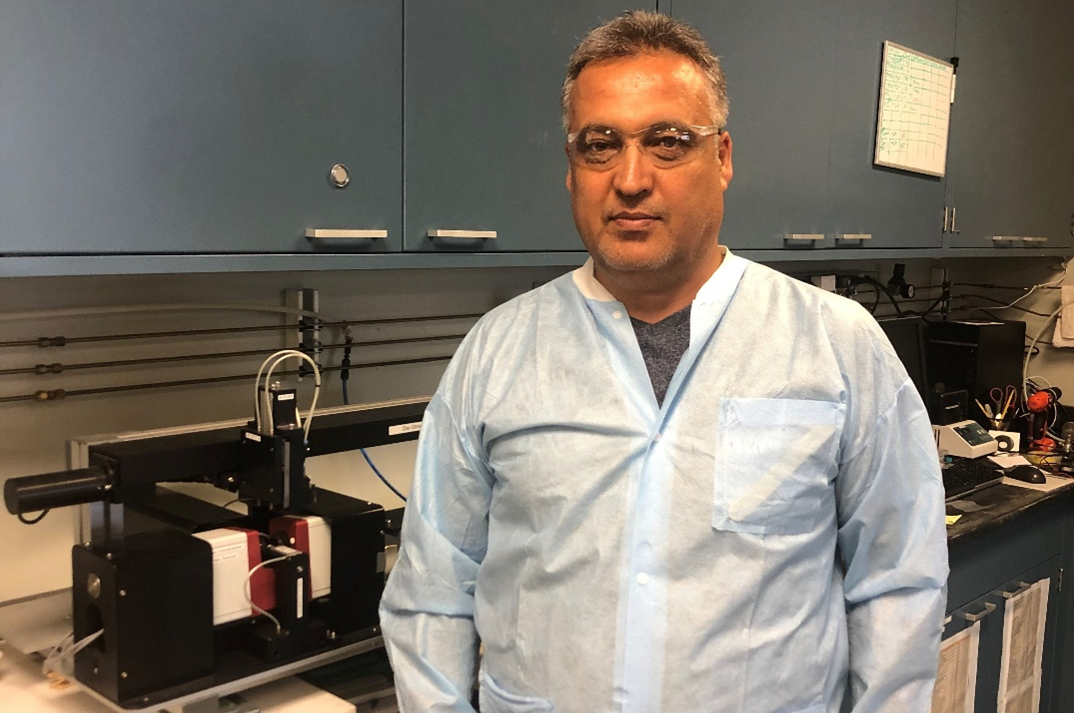